Maximize the Value of Every Asset
You have a lot of expensive equipment in your plant: are you sure they’re all running at maximum efficiency?
You don’t need to fly blind when it comes to your equipment. Spindle helps identify bottlenecks before they compound into bigger problems and improve capacity utilization so your equipment can keep giving you strong outcomes.
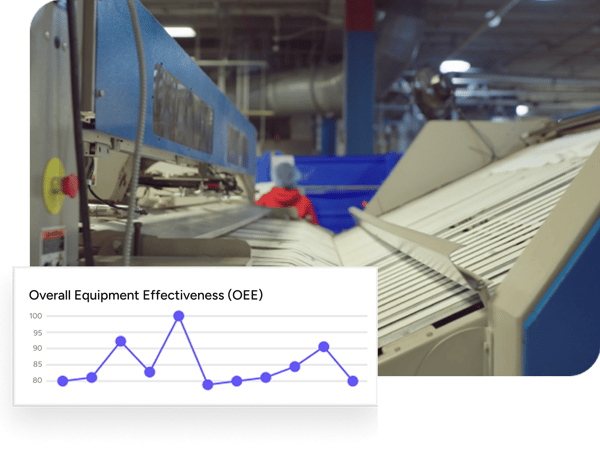
See What's Really Slowing You Down
Know when downtime is driven by equipment issues, operator behavior, or upstream delays.
Quickly find areas in your plant that are slowing your operation.
- Are you changing classifications on a machine too often?
- Is the same equipment consistently going down for maintenance?
- Are your employees performing poorly or is it your equipment?
- How are you tracking your equipment downtime?
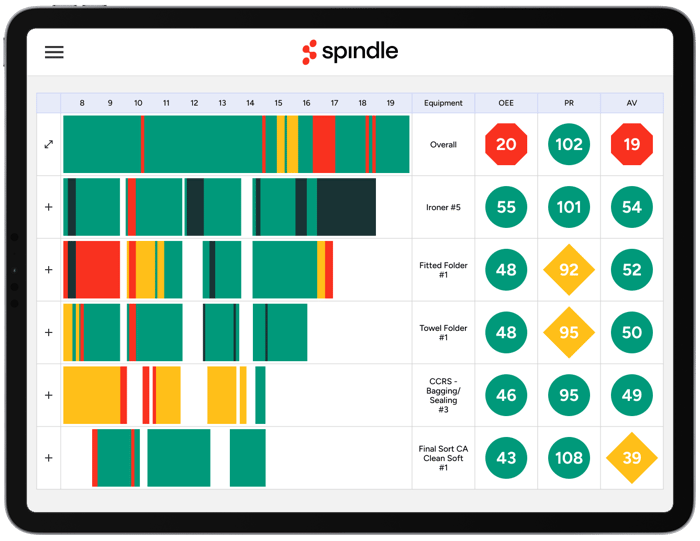
Reveal Where Capacity is Being Lost Down to the Lane.
With an improved visibility into capacity constraints, Equipment utilization simplifies difficult questions like, "Do I need to buy new equipment to meet the additional demands of a new account?"
By displaying true representations of how equipment is being utilized, you can make more informed, data-backed decisions regarding your plant.
Equipment Utilization summarizes capacity losses with the capability to drill down to the equipment and lane level with our OEE dashboard.
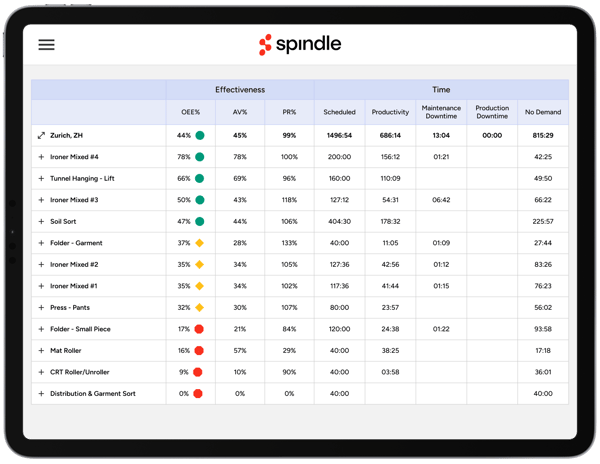
The Best Ability is Availability
Get visibility down to each machine and spot the patterns behind recurring breakdowns.
Equipment Utilization enables you to build smarter preventative maintenance schedules and eliminate repeat failures. Helping your equipment stay running when it matters most.
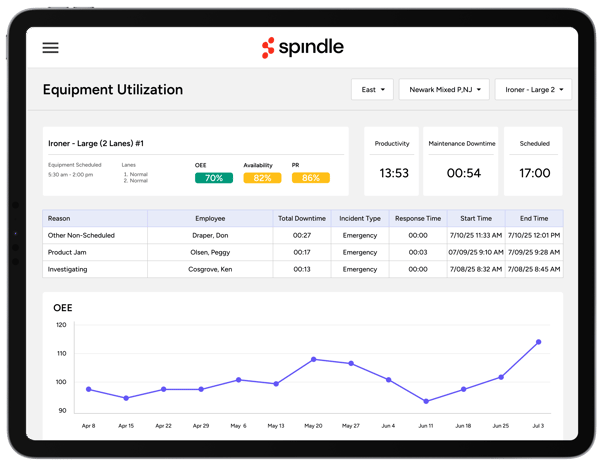
Additional Features
Instant Visibility Into Maintenance Activity
Quickly view where your maintenance team members are logged into around your plant.
Use Historical Data to Stop Repeat Failures
View historical data regarding equipment breakdowns to identify areas employees may need to be coached to prevent product jams.
Real-Time Context for Every Dip in Production
Real-time tracking analysis offers context and reporting for when production is low, such as when maintenance took place, or employees were unavailable.
Trusted by 450+ Commercial Laundries
Spindle was built in the plant, not in a lab. For nearly two decades, we’ve been empowering laundry operators to run smarter, leaner, and faster. Equipment utilization is where it starts.

Hear from Our Customers

“The ongoing monitoring by Spindle and regular feedback with actionable information is what sets them apart.”
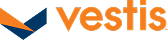
“The PPOH improvement has exceeded our expectations, but more importantly our employees can feel what success feels like because of the real-time feedback and that is priceless.”

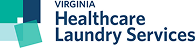
“It is the most invaluable piece of equipment you can install into your plant.”

Ready to Take Your Equipment Usage to the Next Level?
Hundreds of customers have leveraged Spindle to get the most out of their equipment. Reach out to learn more about how you can be the champion of equipment optimization for your operation.